Lean Philosophy: The Key to Business Management
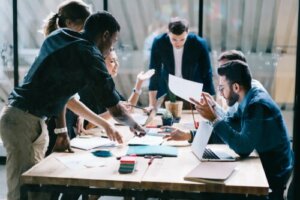
Business management is often the subject of social science research, and there are quite a few theories about how to do it effectively. Today, we’ll talk about an innovative theory that could be the key to improving company productivity and competitiveness. This is Lean philosophy, which has been the key to the success of big businesses all around the world.
Lean philosophy promotes a methodology that provides a new perspective on company goals, strategies, and projects. Also, it provides a framework for corporate philosophy and improves future efficiency and productivity.
If you’re interested in learning more, keep reading. We’ll talk about what Lean philosophy is, where it came from, its main principles, and how it can benefit your business or company.
“If you always do what you always did, you’ll always get what you’ve always got.”
-Henry Ford-
What’s Lean philosophy?
Lean philosophy is a project management methodology that provides tools to help adopt a new, comprehensive approach. Also, it involves innovating processes and improving operational management in order to generate value and benefits.
This philosophy has become the key to assuring corporate survival, which is why it’s so popular. Companies use it to achieve quality and speed. It’s also helpful for aligning the business model with client expectations. In other words, Lean philosophy seeks to eliminate everything that doesn’t add value in order to focus on what’s fundamental to the present moment.
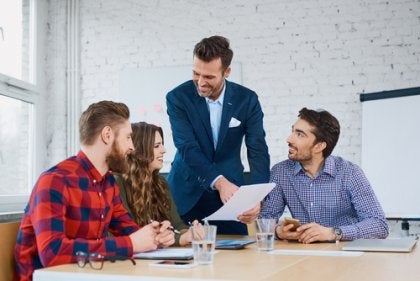
The origins of Lean philosophy
Maybe you’ve never heard about Lean philosophy, but it actually has quite a long history. It turns out that the production system at Toyota, the automaker, was the inspiration for this philosophy.
Everything started with Sakichi Toyoda, who invented the automatic loom. With his creation, he automated not only the work that people previously did by hand but also managed to create a machine that stops itself if a problem occurred, effectively eliminating defective products. As a result, he was able to improve productivity and efficiency.
Later, Kiichiro Toyoda, Sakichi’s son, inherited his father’s philosophy. He proposed a set of ideal conditions so that things work perfectly when machines, buildings, and people work together to add value without creating waste. Kiichiro focused on techniques to eliminate waste. He also fostered automation with a human touch (among other things). Eiji Toyoda, Sakichi’s nephew, enhanced the system by increasing worker productivity.
Eiji Toyoda later provided key support to a man named Taiichi Ohno, who would establish the Toyota production system. They also developed the foundation for the spirit of monozukuri (making things), which led to the method’s brand, called “just in time”.
This system became a world-renowned method. The company continued to improve with the goal of guaranteeing its own evolution. Lately, people usually refer to it as “The Toyoda Way” and many companies have adopted it, inside and outside of the world of car manufacturing.
Where did the name come from?
We have Daniel T. Jones, Daniel Roos, and James P. Wockmack to thank for the name of this philosophy. They wrote a book called The Machine That Changed the World: The Story of Lean Production. They coined the term that we know today.
In the book, they talk about Toyota’s production system. Today, they offer a guide for managers and industry leaders who are looking to transform traditional businesses into successful examples of Lean philosophy.
The basics of Lean philosophy
Lean philosophy has several principles that your business should adhere to. They’re effectiveness, quality, and productivity, among others. Here are the most important principles in more detail:
- Continuous improvement – Kaizen. Every step represents progress. After every process, you should ask yourself “How can we make this better?”, “In what ways has the process failed?” and “What’s essential and what isn’t?”
- Detecting and solving problems. This involves paying attention to what’s happening in order to quickly find mistakes and problems. Thus, you solve the main issue, which helps productivity. This also satisfies the clients’ demands for high quality.
- Optimize the system. Improving the possible results by emphasizing management, planning, processes, movements, excess production, quality, and defects.
- Eliminate waste. If something isn’t contributing to the business, get rid of it. In other words, if it isn’t generating benefits, it’s useless.
- Quality built-in. All of the projects have to be oriented towards quality. Working this way guarantees a competitive advantage through demand capacity.
- Value chains. Divide the project into distinct, connected stages, with the option to make changes along the way. The goal is for the product to evolve as it moves through the different stages.
- No guessing. Promoting a system of stages makes it easier for the business to respond to the real demands of the client. Value chains make this possible.
The 5S strategy
Applying Toyota’s 5S strategy is also useful for achieving lasting change. They are:
- Seiri (sort). Subordinating, classifying, and eliminating.
- Seiton (systematize). Organizing.
- Seiso (shine). Focusing on cleaning things up.
- Seiketsu (standardize). This highlights simplification, making things coherent.
- Shitsuke (sustain). Sustain the process through discipline.
All of these principles contribute to business success. You could also follow Ohno’s advice, which has endured throughout history. Ohno was focused on attacked waste. If you see any of the following in your company, you know where to start:
- Over-processing.
- Repetitive work.
- Movement of people that doesn’t add value.
- Producing goods when there’s no demand.
- Movement of inventory that doesn’t add value.
You should also keep in mind that, when workers find themselves doing the same amount of work, something’s wrong. That’s why it’s so important to keep your full attention on every aspect of your business. This is the key to optimizing production.
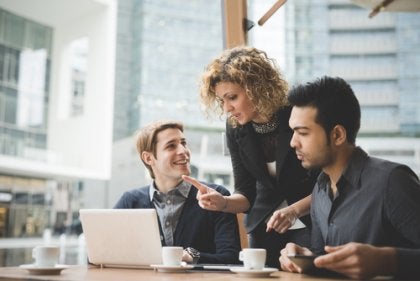
The benefits of implementing Lean philosophy in your business
Implementing Lean philosophy in your business will bring important gains. We aren’t just talking about financial gains, either. If you want to make it happen, you should know that it takes a lot of hard work. It’s not as simple as it sounds because you have to make some significant changes. Nevertheless, with some effort and dedication, you’ll achieve your goal.
Here are some of the benefits of applying this philosophy:
- The employee feels a sense of belonging.
- Your employees will feel more motivated.
- The useful life of your teams will increase.
- The company will produce higher-quality products.
- Time-optimization.
- Goodbye to wasted time and useless meetings!
- Increased company value.
- Gain new customers.
- Optimize your system.
- Improve your business’s longevity.
- Problem-solving through continuous improvement and learning.
- Improve the workplace environment.
- Economic growth.
- Stability with the organization’s members.
- Avoid the kind of excess production that often leads to losses.
- Create leaders that can teach this philosophy to others.
- The formation of teams who follow the business’s philosophy.
In conclusion
Lean philosophy creates long-term projects that promote learning. They also encourage improving the process to avoid making the mistakes that lead to losses. So, you learn from the mistakes you make.
Many, many businesses use this philosophy. You can find examples of those businesses in the Journal of Lean Systems. For example, Garcia, Santos da Silva, and Antonowicz published an article in 2019 that discusses Lean tools applied to urban public transportation. Their study found that Lean philosophy brings improvements because it eliminates errors and waste. That also increases value, not only for the business but for the customer as well.
Thus, Lean philosophy can help you achieve optimal business management. If you apply this methodology, you’ll have to get to know your business, its processes, your employees, and your machines like the back of your hand. That will help you improve what isn’t working well and see major results.
Lastly, Toyota has become a large and extremely successful company because of these ideas. The company’s famous “kaizen” (continuous improvement) motto also plays an important role. Follow its example, and overcome your business’s obstacles by always looking for ways to optimize your system. Lean philosophy could be the key to your company’s success. Why don’t you give it try?
All cited sources were thoroughly reviewed by our team to ensure their quality, reliability, currency, and validity. The bibliography of this article was considered reliable and of academic or scientific accuracy.
García, J.R., Da Silva Zagheni, E.S., & Antonowicx, M.A. (2019). Lean tools applied in urban public transportation. Journal of Lean Systems, 4 (1), 154-173.
Lu, J. (2018). ADN. Filosofía Lean para Desarrollar, innovar y superarse en Crear Valor y Beneficios. Universidad nacional de Ingeniería.
The origin of the Toyota Production System. A production system that has been fine-tuned over generations. Roots of the Toyota Production System. Recuperado de https://www.toyota-global.com/company/vision_philosophy/toyota_production_system/origin_of_the_toyota_production_system.html, el 21 de enero de 2019.
Womack, J.P., Jones, D.T., & Ross, D. (1990). Machine that changed the world. Nueva York, Estados Unidos: Simon and Schuster.
This text is provided for informational purposes only and does not replace consultation with a professional. If in doubt, consult your specialist.